Respiratory Protection and Mask Fit-Testing
While the elimination or reduction of the need for respiratory hazards through substitution or the use of engineering controls is preferred, there may be situations where these controls do not exist, are not practicable, are temporarily ineffective because of equipment availability or do not fully eliminate the hazard. In these cases, respiratory protection may be required.
Respiratory protective equipment is required when workers perform tasks in atmospheres that are: oxygen-deficient, contain airborne particulates above occupational exposure limits (OEL) or at levels considered to be hazardous.
The university has established the (google doc) Respiratory Protection and Fit-Testing Program (external link) to outline the requirements for the selection, use and care of respirators. This program will assist in the proper selection of respirator cartridges and filters that are appropriate for the irritant/particle/chemical vapours present. It will also provide guidelines for fit-testing to ensure the respirator fits the user correctly and is properly sealed against the user’s face.
This program applies mainly to tight-fitting air-purifying respirators.
This program does not apply to:
- supplied air respirators as TMU community members should not be working in oxygen-deficient environments or be exposed to toxic gases immediately dangerous to life or health (IDLH) atmospheres
- non tight-fitting surgical masks (e.g., disposable medical/surgical masks, cloth masks)
Getting started
Hazard Assessment
In order to determine the presence of a respiratory hazard and to assist in the selection of an appropriate respirator, a hazard assessment of the work area will be conducted by the supervisor in consultation with EHS. The assessment of a respiratory hazard uses the hierarchy of controls (see diagram below) and includes the following:
- Identification of contaminants present in the workplace
- Identification of physical states of airborne contaminants
- Determination of the likelihood of inhalation of the contaminants
- Measurement or estimation of the concentration of the contaminants
- Identification of the established occupational exposure limit for each airborne contaminant
- Determination of whether the atmosphere is immediately dangerous to life and health (IDLH) including oxygen deficiency
- Determination of applicable health regulation or a substance-specific standard for the contaminants
- Determination for particulate hazards if there is oil present
- Determination of skin or eye absorption and irritation characteristics.
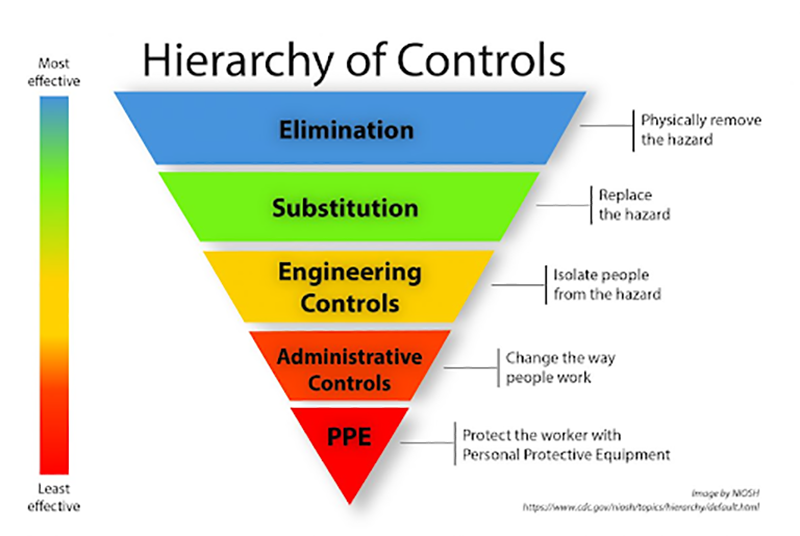
Respirator User Screening
As certain medical conditions may impact an individual’s ability to safely wear a respirator, prior to fit-testing and respirator use, a user must complete a screening form and, where certain health conditions exist, discuss respirator use with a physician.
Respirator users are required to complete the Respirator User Screening Questionnaire (external link) , which will be reviewed by EHS, prior to fit testing and respirator use. Personal health information need not be provided on the form.
Respirator Use and Accommodation
The university’s Discrimination and Harassment Prevention Policy and the Ontario Human Rights Code may require the university to accommodate individuals where using a respirator creates a barrier related to one or more of the protected grounds under the policy, including for example disability/health condition or creed/religion. Accommodation needs should be identified on the Respirator User Screening Questionnaire.
Medical Surveillance
If the screening questionnaire identifies a health condition that may be incompatible with the use of a respirator, EHS will notify the intended respirator user about the need for an assessment conducted by a physician. The worker, their leader and EHS shall provide the physician with information regarding the conditions of respirator use and the type of respirator(s) required.
After the medical evaluation, the physician shall complete the clearance letter (external link) indicating one of the below options and return the form to Workplace Wellbeing Services (HR).
- User meets medical requirements to use the respirator
- User does not meet medical requirements to use the respirator
Workers who are cleared to work with respirators may then proceed to fit-testing. Workers who do not meet medical requirements to use a selected respirator shall not work in an area where the use of a respirator is required. The accommodation process shall then be followed, led by Workplace Wellbeing Services (HR).
Respirator Fit-Testing
There are two types of testing available for respirator fit testing. Upon completion of the Respirator User Screening Questionnaire (external link) , EHS will schedule a fit test appointment. Workers must not chew gum, smoke, eat or drink anything other than plain water for 15 minutes prior to fit testing.
A fit test shall not be performed unless the person undergoing the test is clean-shaven, where the facepiece seals to the skin. When other personal protective equipment, such as eye, face, head and hearing protectors, are required to be worn, they shall be worn during the respirator fit tests to confirm that they are compatible with the respirators and do not break the facial seal.
A respirator fit-testing form, documenting the results of the fit test shall be completed by the fit tester and retained by EHS and supervisor. A respirator fit testing certificate will be issued to the user upon successful completion of the fit test. The fit test certificate documents the following:
- name of the person tested;
- make, model and size of the respirator fitted;
- fit test expiry date;
- person conducting the test.
Loose-fitting masks, like surgical masks, are mainly used for protection against droplets (not airborne contaminants). They do not require a tight seal with the face to provide protection. Therefore, they do not need to be fit tested.
Qualitative Fit Test
For tight fitting respirators, fit testing is required before using a respirator for the first time. A qualitative fit test is the most common type of test and covers most of the regularly used workplace masks such as N95, half face and full face respirators. The test involves the taste sensitivity of the person being tested and can be applied to any type of mask that does not have its own separate air supply. The tests can only be performed by a qualified fit tester.
Fit-Test Frequency
A new fit-testing is required when there is a change in the following as recommended:
- when changes to a user’s physical condition (e.g., significant weight change or changes to facial or dental features, pregnancy-related weight change) could affect the respirator fit;
- when there is a change in respirator (e.g., make, model, size);
- when a respirator user experiences continued significant discomfort during use or difficulty in completing a successful user seal check;
- when there is a change in PPE use that could affect the respirator; and
- at least every two years.
Respirator Selection
Respirator Types
Respirators vary in design, equipment specifications, application and protective capability and these factors shall be considered in respirator selection. Respirators fall into two main classes; air-purifying respirators (APRs) and supplied-air respirators (SARs).
Air-purifying respirators (APR)
- Tight-fitting (e.g., N95 respirator)
- Powered air purifying respirator (PAPR)
Air purifying respirators use mechanical or chemical filters to remove air contaminants in the inhaled air. Particulates (e.g., fibres, metal fumes, dust) are removed by mechanical filters that are made from polyester/cellulose/polypropylene type materials. Gases and vapours, including organic vapours, are removed by cartridges containing a sorbent (activated carbon). These chemical cartridge filters purify air by adsorbing or neutralizing gases or vapours on a sorbent (adsorbing material) in a cartridge.
Note: Wearing a respirator with a particulate filter (e.g., a N95 respirator) is not effective in protecting against gases or organic vapours.
There are reusable and disposable masks. Reusable tight-fitting respirators typically come in as half-mask or full facepiece.
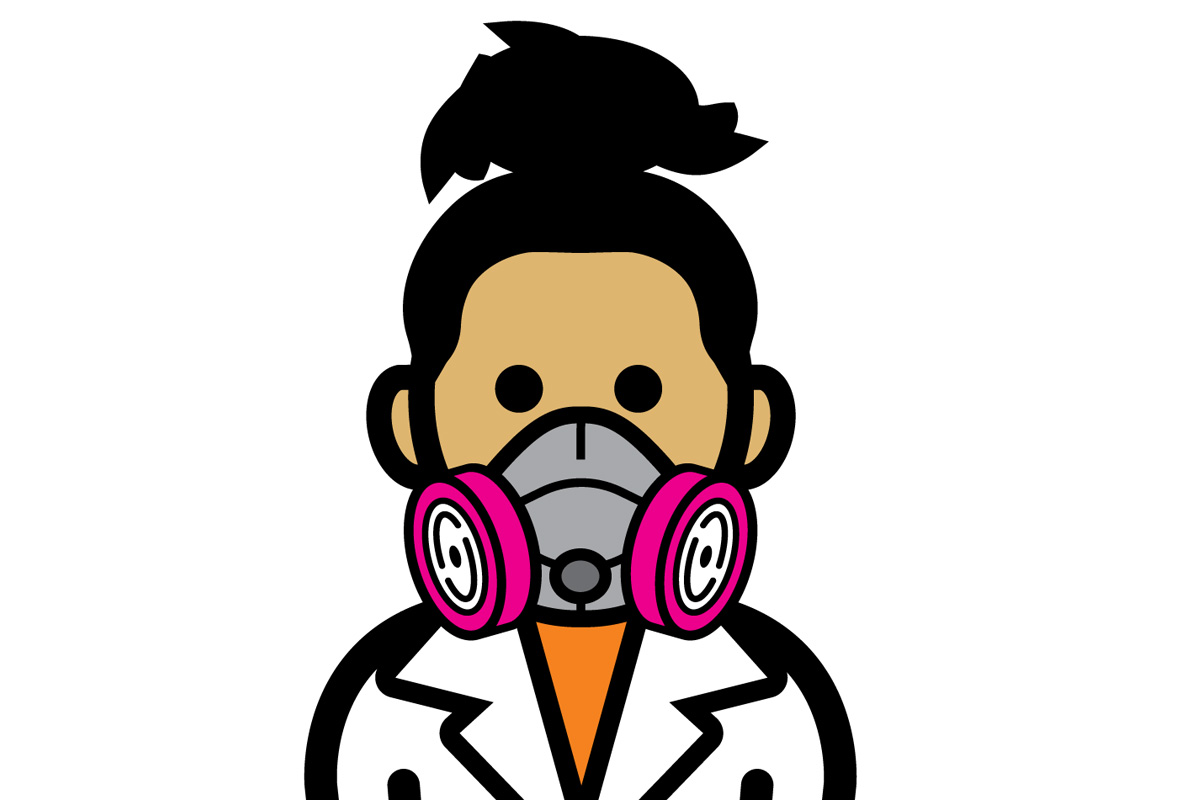
Half-mask
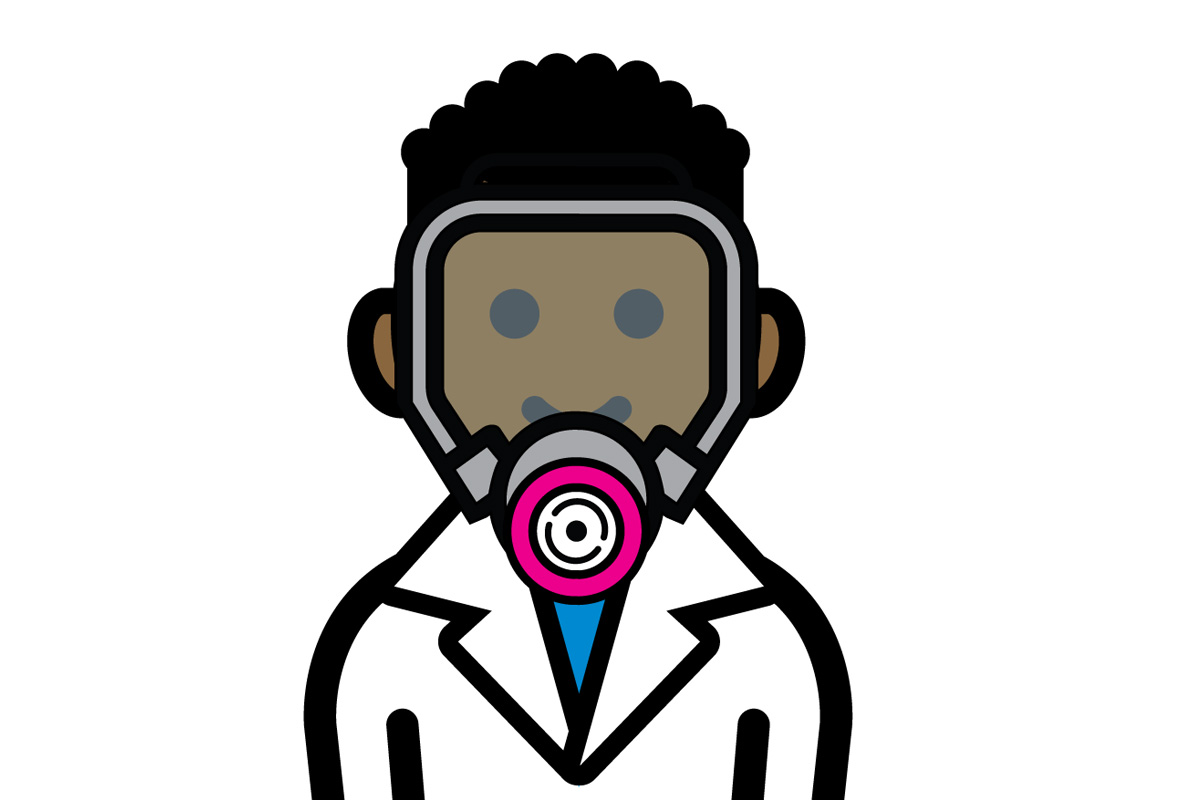
Full facepiece mask
Air-purifying respirators have limitations and should not be used where
- there is insufficient oxygen (less than 19.5%)
- very high concentrations of contaminants are present.
There are different classes of particulate filters, depending on the particulate material:
- "N Series", which means not resistant to oil;
- “R Series”, which means resistant to oil; and
- “P Series”, which means oil-proof.
A mask with an N95 rating is not resistant to oil and has a 95 percent filter-efficiency rating. Filter efficiency means the percentage of particulates removed by the filter. There are three levels of filter efficiency: 95 percent, 99 percent and 99.97 percent. The higher the efficiency, the lower the leakage when properly fitted and worn.
Respirator Selection Process
Respirators must be selected in consultation with EHS and in accordance with CSA Standard Z94.4. Users may only use respirators for which they have been fit tested as required, trained, and have been deemed fit to use.
Equally important is the selection of the correct type of cartridge or filter. Filters are made of material that is designed to trap particles as you breathe. Cartridges contain a material that absorbs gases and vapours. It is very important to make the appropriate filter or cartridge that is being used for the chemicals or substances present in the workplace. Before using or handling a hazardous product, consult the safety data sheet (SDS) for the type of respiratory protection required.
A detailed process on respirator selection can be found in the (google doc) Respiratory Protection and Fit-Testing Program manual (external link) .
Respirator Seal Check
To ensure a proper fit, a seal check should be performed each time a respirator is worn. Test for fit every time you put the respirator on and throughout your shift. Two easy tests can show whether most reusable respirators fit right and don’t leak.
Please refer to the Respirator Protection Program manual for the details on both
- negative-pressure seal check
- positive-pressure seal check
Recordkeeping
Supervisors will retain the following records:
- Respirator User Screening Questionnaire (retain copy from user)
- Respirator fit-testing form
- Training
- Safe work procedures for respirator maintenance and care
- Safe work procedure on cartridge/filter change schedule
Legislation
The Respiratory Protection and Fit-testing program is written in accordance with the requirements of regulations under the Ontario Occupational Health and Safety Act, as well as the Canadian Standards Association (CSA) Standard CAN/CSA-Z94.4 and R.R.O. 1990, REGULATION 833: Control of Exposure to Biological or Chemical Agents (s.9-13 Respiratory Protection Program).