Turning old wind turbine blades into something new
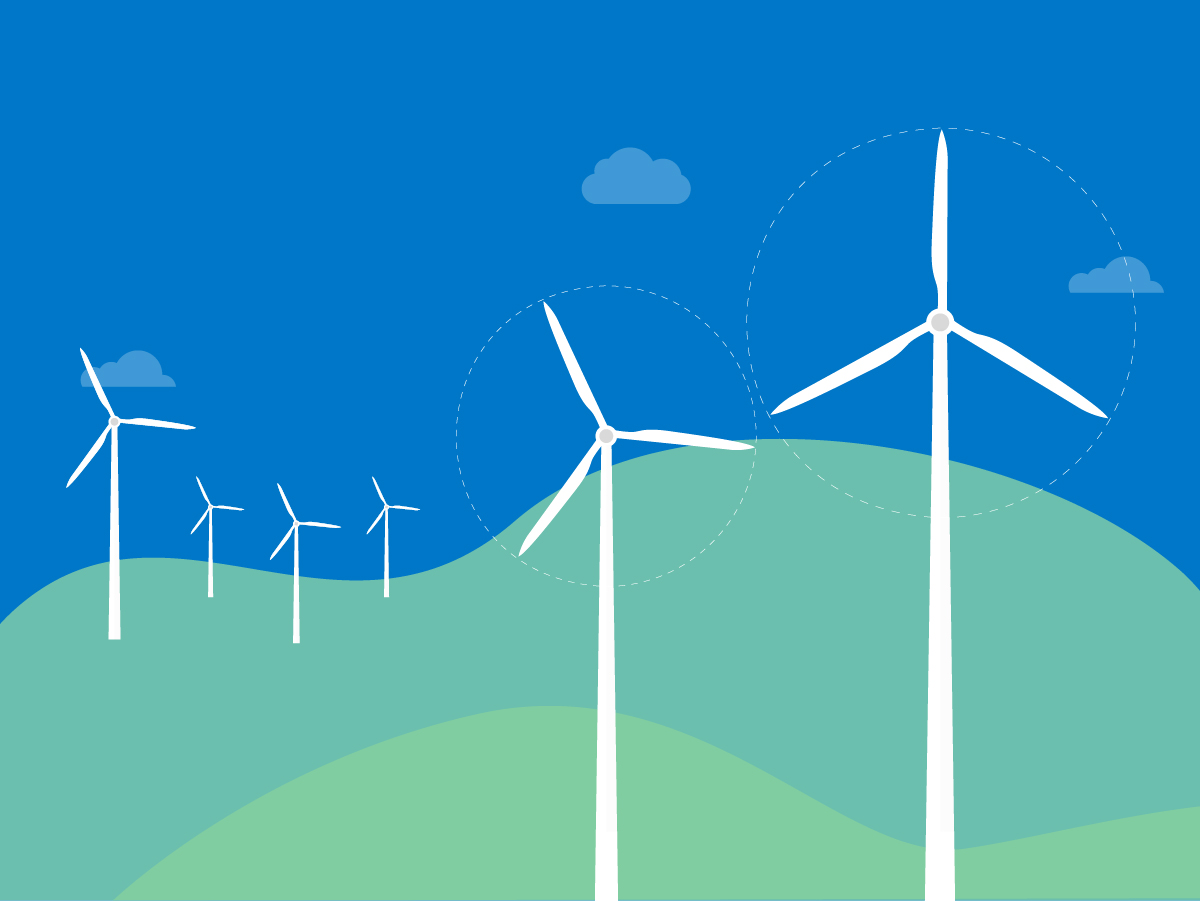
Kazem Fayazbakhsh, a professor in the Department of Aerospace Engineering specializing in materials science, says he and his team have come up with a recycling solution to the growing problem of turbine blade trash that could ultimately help create a circular economy for wind energy.
The rapid rise of renewable electricity as a way to wean the world off climate-warming fossil fuels has been rightly heralded as a net-positive for the planet. But there are still environmental concerns with some of these green technologies that need to be addressed.
Take wind energy. Wind turbine blades typically last around 20 years and after decommissioning are mostly headed for the landfill. However, a Ryerson University researcher is helping to make this form of clean power even cleaner by using the latest 3D manufacturing technologies to give the blades a second life.
Kazem Fayazbakhsh, a professor in the Department of Aerospace Engineering specializing in materials science, says he and his team have come up with a recycling solution to the growing problem of turbine blade trash that could ultimately help create a circular economy for wind energy.
“Landfilling is a major way of getting rid of these wind turbine blades in the United States and Canada,” said professor Fayazbakhsh. “Twenty or 30 years ago, they didn’t think about the end of life. But now, companies have started thinking about what's going to happen at the very end.”
“We saw that we can address this challenge by looking at another advanced manufacturing technique, which is 3D printing,” he said. “I work on what they’ve called ‘the complete cycle of 3D printing’.”
Working in Ryerson’s state-of-the-art Facility for Research on Aerospace Materials and Engineered Structures, (FRAMES) professor Fayazbakhsh’s research team has managed to design, test and demonstrate a new composite material using wind turbine fibreglass waste.
His team takes an end-of-life blade and grinds it down before sorting, categorizing and extruding the particles into a polymer. The resulting filaments are then fed into the lab’s industrial-scale 3D printers to create parts that are widely sought by a variety of industries.
It’s the enduring strength and stiffness of the turbine blade fibres that make them such an attractive proposition to work with, notes professor Fayazbakhsh. “We knew that they were very strong and that’s good for us, because we can use those very strong fibres to reinforce the polymer, increasing structural performance. The process worked very well because we were able to essentially make new filaments with reinforced recycled glass fibres, and test their properties, to show the improvement that you can get.”
The results from the lab, published in several scientific journals (external link) , are so promising that professor Fayazbakhsh has spun out a company, Fibrecycle Materials Corporation, to commercialize the process. He is already working with organizations, including fibreglass suppliers, automakers and technology companies, among others, to create parts for their products.
“There’s a lot of interest in industry, especially with all the recent issues with the supply chain. You can do all the manufacturing close to where you want to use it,” he said. “We have shown that this process works, and our next step is raising capital and doing a project at the industrial-scale – let’s say recycling 40 to 50 tonnes of products – and showing that this can be done.”
In addition to its wider applications, the ultimate goal of the research is to drive sustainable change in the industry by working with turbine manufacturers and operators to return end-of-operation blades back into the same system from which they originated – recycling them over and over again – and building a circular economy.
“[Green wind energy] is the new way of powering the planet, so we need to really understand it. What happens to these blades is a major issue that is only going to get worse. I always tell my students that we do research not just for research, but to work on real life problems.”
Professor Fayazbakhsh’s 3D printing research is supported by funding from the Natural Sciences and Engineering Research Council of Canada through its Discovery and Alliance grants.
Larry Lessard, professor of mechanical engineering at McGill University, also contributed to the research.